Project description
In early 2018, construction began on the new terminal for loading and transporting salts and potash for Tráfico de Mercancías (Tramer), a subsidiary of ICL, at the Álvarez de la Campa pier in the Port of Barcelona.
ICL, a multinational mining company, is both the promoter and operator of these facilities. The construction was awarded to a joint venture formed by the construction companies DRAGADOS and SORIGUÉ, which subcontracted the production and installation of polypropylene fiber-reinforced concrete to PROMSA. This concrete was used to pave both the interior surfaces of two new warehouses (about 30,000 m²) and the exterior urbanization of the terminal (another 30,000 m²). In total, 60,000 m² out of the terminal's total surface area of 81,000 m² were paved.
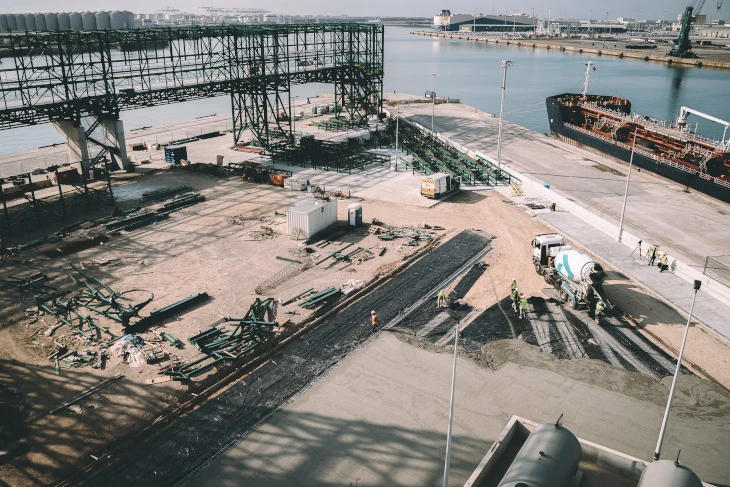
The challenge
The concrete used for the pavement needed to have specific characteristics: it had to withstand the load of storing salts and potash, resist chloride attacks from both the materials and the marine environment, and ensure high durability. To meet these requirements, polymer fibers were used to reinforce the concrete instead of traditional steel mesh.
The use of fibers allowed for concrete with high flexural strength, and choosing polymer fibers prevented chloride attacks. Additionally, using corrugated fibers resulted in higher residual strengths.
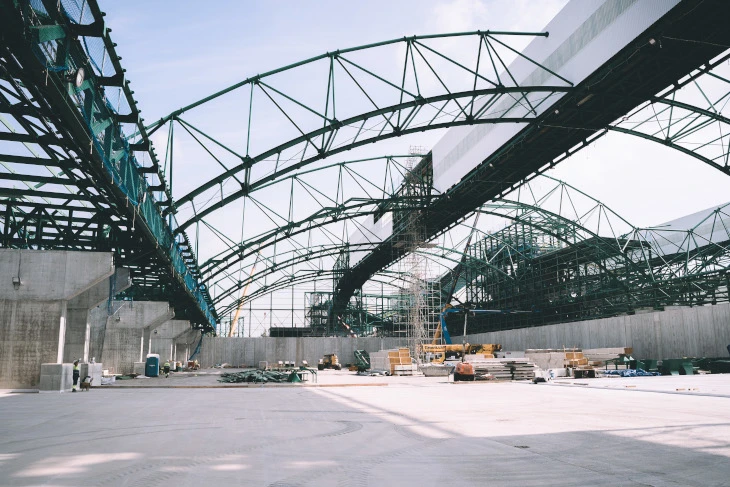
Our solution
The concrete supplied was designed for both an exterior pavement and an interior overlay of the storage warehouse. The concrete incorporates MasterFiber 249 polymer fibers at dosages of 5 kg/m³ and 4 kg/m³, respectively, with a water/cement ratio below 0.45 and a slump of no less than 18 cm, stable for up to 3 hours (the anticipated transportation and execution time). To meet all these requirements, the superplasticizer additive MasterEase was used, allowing for high water reduction while maintaining extended workability.
Our Technical Service actively participated in the design of the concrete, as well as in its validation phase, in coordination with the concrete producer, PROMSA. This approach quickly achieved the goal, building full confidence with both the contractor and the owner.
Clients benefits
The MasterEase admixture solution proposed by Master Builders Solutions met the specific on-site requirements, achieving a 30% reduction in concrete viscosity, improved workability, extended slump retention, and reduced water addition.
Using structural polymer fiber in this project resulted in a 50% labor cost savings and lower maintenance costs due to the non-corrosive nature of the finished pavement.
This approach minimized operational costs for the concrete producer while meeting the contractor's and owner's demands. The support from our Technical Service was crucial in ensuring the correct use of admixtures, building trust, and facilitating the project's smooth progression to completion..
Project highlights
Full compliance with quality and durability requirements was achieved through the careful selection and use of the proposed fibers and admixtures, as well as close collaboration between PROMSA's Quality Department and the Technical Service of Master Builders Solutions.
Rapid execution system, without the need for metal mesh, spacers, or concrete pumping, allowed direct access to all areas for pouring.
Using polymer fiber resulted in a 40% reduction in CO2 emissions compared to conventional metal mesh solutions, adding value in terms of sustainability.