Antecedentes
A principios de 2018 se inicia la construcción de la nueva terminal de carga y transporte de sales y potasas para Tráfico de Mercancías (Tramer), filial de ICL, en el muelle Álvarez de la Campa del Puerto de Barcelona.
La multinacional del sector de la minería ICL es la promotora y explotadora de estas instalaciones, cuya construcción es otorgada a la UTE formada por las constructoras DRAGADOS y SORIGUÉ, que subcontrata a la empresa PROMSA la producción y ejecución del hormigón reforzado con fibras de polipropileno para pavimentar tanto las superficies interiores de los dos nuevos almacenes (unos 30.000 m2), como la urbanización exterior de la terminal (otros 30.000 m2). En definitiva, se pavimentan 60.000 m2 de los 81.000 m2 que conforman la superficie total de la terminal.
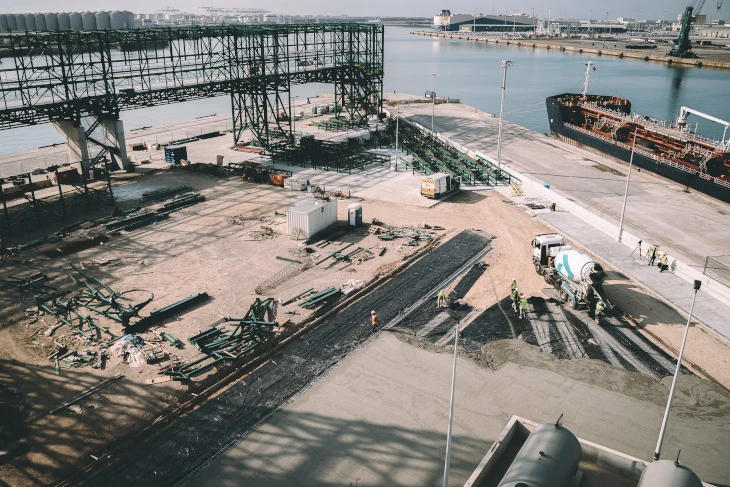
El reto
El hormigón empleado para la ejecución de los pavimentos debe reunir unas características únicas: debe ser capaz de soportar las cargas de almacenaje de sales y potasas, resistir el ataque por cloruros dado por el propio material como por el ambiente marino en el que se encuentra, y garantizar una alta durabilidad. Por estos motivos, se plantea el uso de fibras poliméricas como refuerzo del hormigón en lugar del tradicional armado con mallazos.
El empleo de fibras permite conseguir hormigones con alta resistencia a flexotracción, optar por fibras de naturaleza polimérica impide el ataque por cloruros y, finalmente, que sean corrugadas permite obtener resistencias residuales mayores.
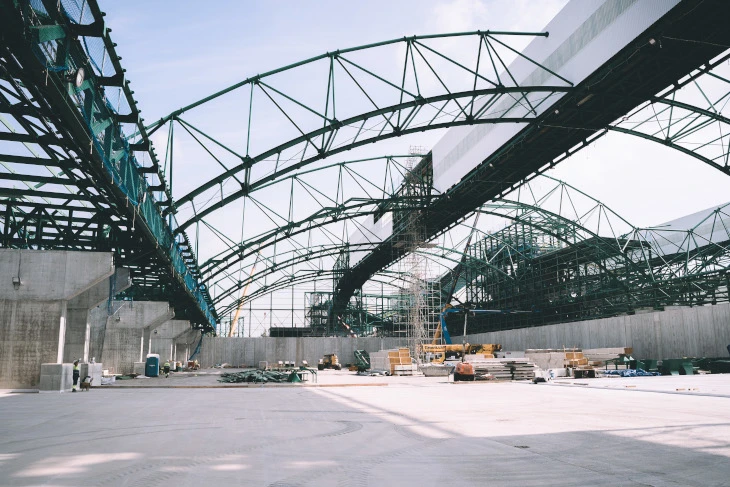
Nuestra solución
El hormigón suministrado se diseña para ejecutar tanto un pavimento exterior como un recrecido interior de la nave de acopio. El hormigón incorpora fibras poliméricas MasterFiber 249 con una dosificación de 5 kg/m3 y 4 kg/m3 , respectivamente, con una relación agua/cemento inferior a 0,45 y una consistencia no inferior a 18 cm, estable durante períodos de hasta 3 horas (tiempo de transporte y ejecución previsto). Para conciliar todos estos requisitos se emplea el aditivo superplastificante MasterEase que permite una alta reducción de agua en combinación con la necesidad de un mantenimiento prolongado de la trabajabilidad.
Nuestro Servicio Técnico participó activamente en el diseño del hormigón así como en la fase de validación del mismo, en coordinación con el productor de hormigón PROMSA. De este modo enseguida se alcanzó el objetivo, generando confianza plena con el constructor y el propietario.
Beneficios para el cliente
Con la solución del aditivo MasterEase propuesta por Master Builders Solutions se consigue cumplir con los específicos requerimientos de puesta en obra, una reducción de la viscosidad en un 30% del hormigón, mejora en la trabajabilidad, aumento del mantenimiento de consistencia y reducción del añadido de agua.
La alternativa ejecutada en esta obra mediante el uso de fibra polimérica estructural aporta un ahorro del 50% en mano de obra y una reducción de los costes asociados al mantenimiento posterior, debido a la no corrosión del pavimento ejecutado.
Todo ello permite minimizar los costes de operación del productor de hormigón y satisfacer las exigencias de la empresa constructora y el propietario de la infraestructura.
El soporte prestado por nuestro Servicio Técnico fue clave para el correcto uso de los aditivos necesarios para satisfacer los requisitos demandados al hormigón, en el mínimo tiempo y con una regularidad infalible. Este aspecto resultó clave para generar confianza y permitir una cómoda evolución del proyecto hasta su conclusión.
Lo más destacado del proyecto
Pleno cumplimiento de las exigencias de calidad y durabilidad gracias a una adecuada selección y uso de las fibras y aditivos propuestos, y gracias al trabajo conjunto del Dept. de Calidad de PROMSA y el Servicio Técnico de Master Builders Solutions.
Sistema de rápida ejecución al no disponerse mallazo metálico, separadores, ni necesidad de bombeo del hormigón ya que se puede acceder con el camión directamente a todas las zonas, para hormigonar por vertido directo.
El empleo de fibra polimérica provoca una menor huella ambiental (menores emisiones de CO2, reducidas un 40% respecto a soluciones convencionales con mallazo), confiriendo al producto un valor añadido en términos de sostenibilidad.