MasterAtlas®, Virtual Concrete Assistant, Facilitates Reuse of Returned Concrete
John Gallagher
Master Builders Solutions US & Canada
How concrete producers can resell more returned concrete with instant and accurate MasterSet DELVO admixture dosage recommendations.
Returned concrete can account for up to 10% or more of concrete batches, equating to a loss that extends far beyond just materials. It's a multifaceted problem eating away at operations capacity, profits, and sustainability goals.
Traditional tactics, from crushing to block forming, not only increase expenses, but they also fail to align with today’s environmental and operational imperatives, and often cause more harm in terms of safety issues, space requirements, labor hours and disposal.
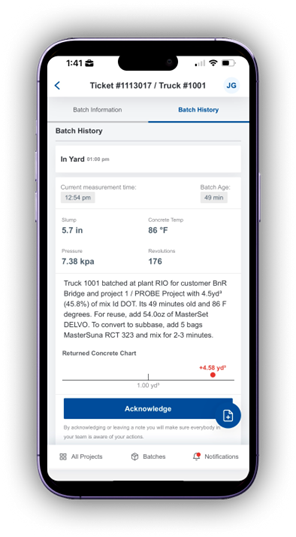
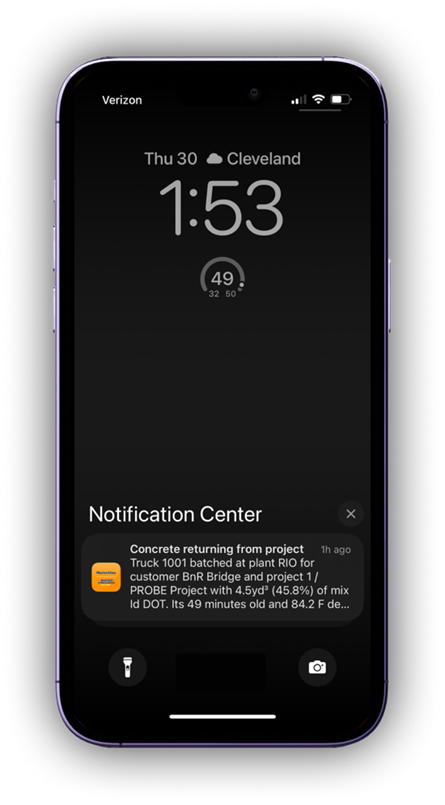
Instant MasterSet DELVO Recommendations: For each batch of returned concrete, MasterAtlas delivers instant, customized by local materials, dosage recommendations directly to your dispatchers or batch personnel through their phone, or Microsoft Teams, if equipped.
There is no need for visual checks or manual data entry; everything is automated and communicated in real-time, enhancing operational efficiency.
Master Builders Solutions Expertise: Rest assured that MasterSet DELVO admixture recommendations, sent directly to dispatchers, have been designed specifically for each plant, including dosage adjustment based on batched materials or included line items.
Significant Cost Savings: The potential to save $22,000 per truck annually by utilizing returned concrete presents a compelling financial incentive for concrete producers.
Reduced Environmental Impact: By reusing returned concrete, producers can significantly lower their carbon footprint, conserving a valuable resource by utilizing 50% less virgin material.
Operational Efficiency: The automation of determining reuse suitability, calculating dosages for treatment, and integrating with dispatch systems streamlines operations, reducing the time and resources needed to manage returned concrete.
Material Cost Recovery: The Returned Concrete System allows for the recovery and reuse of materials from returned concrete, further reducing waste and contributing to cost savings.
Traditional Methods | With MasterAtlas® |
Manual reading and paper chart tools, slowing decision-making for use of returned concrete, leading
to inefficiencies and potential errors. | Automated assessment of returned concrete for immediate determination of reuse options. |
Significant operational challenges in managing returned concrete, including
disposal costs
and environmental concerns. | Streamlined operations with reduced manual intervention, freeing up resources for other tasks, and
keeping trucks moving concrete to customers. |
Limited options for reusing returned concrete, often resulting in it being wasted or used in less valuable applications. | Increased ability to reuse concrete, both as material and in new concrete batches, maximizing resource utilization. |
Environmental impact of disposal practices and the
opportunity cost of materials lost in the process. | Improved environmental sustainability through reduced waste and CO2 emissions, by using up to 50% less virgin rock/materials. |
Discover how easy it is to save significant money, resources and time while meeting sustainability goals using MasterAtlas, virtual concrete assistant to manage returned concrete.
Contact us for a free trial. No “downloads" or “installs," just login and execute on day 1.