Client: | Scottish Government |
---|---|
Main contractor: | Forth Crossing Bridge Constructors |
Concrete producer: | Forth Crossing Bridge Constructors |
The challenge
The main challenges in such a large non-stop process were logistical: ensuring a constant supply of raw materials to the batching plant and the use of established batching procedures ensured that the right quality of concrete was produced.
The operation to infill the tower caissons with underwater concrete was the subject of detailed planning for many months.
On completion, the pour caissons were emptied of water, cleaned and prepared for the next stage of construction – the creation of reinforced structural concrete foundations that will support the three 210m-high towers.
Our solution
FCBC worked extensively with Master Builders Solutions to design and deliver a mix capable of being specification compliant whilst providing high strength, consistent workability, long retention times and high flow characteristics. The challenges posed by the project resulted in the development of MasterGlenium SKY 903, engineered to allow high levels of water reduction and extended workability retention, without sacrificing early strength development performance or having any negative effect on the construction program. Preliminary laboratory work identified that incorporating a modern generation set retarder MasterSet R 200, gave further confidence and concrete uniformity, enhancing placing and finishing operations.
The south tower underwater concrete plug involved a continuous 15-day operation with concrete being poured into a mass foundation 24 hours a day. After batching, the concrete was delivered by a continuous flow of 8m³ loads to the quayside and pumped onto purpose-built bespoke barges, each capable of carrying a total of 72m³, with six static 12m³ concrete mixers on deck. The concrete was then pumped from the barges into the foundation caissons through a special floating tremie pipe. Concrete ‘flowed’ approximately 20 metres under hydrostatic pressure and settled correctly, with any trapped air driven up to the surface as the concrete rose.
FCBC had to consider possible delays such as weather and breakdowns; a set retarder (MasterSet R 200) was used to provide extended retention times in excess of 12 hours. As the concrete level rose, the seawater inside the caisson was displaced.
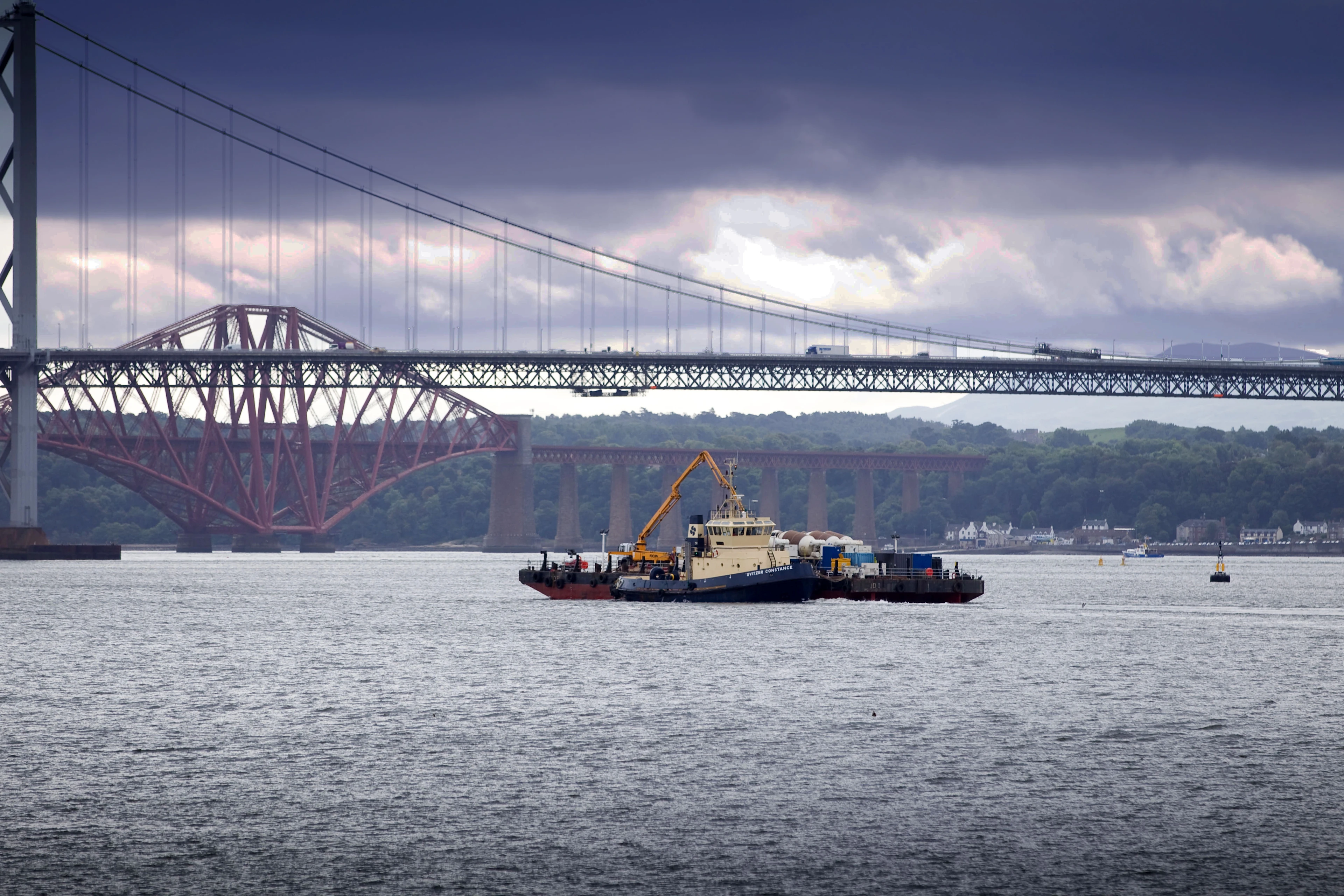